Предпосылки появления бережного производства
Мы не будем углубляться в историю основания компании Toyota, хоть она весьма увлекательна. Это дело рук людей, которые не просто кропотливо занимались своими обязанностями, а стремились совершенствовать производственные процессы и инструменты работы. Поэтому неудивительно, что в этой компании смогли создать революционный подход к производству.
Послевоенные годы для Японии были весьма тяжелыми, потому что приходилось восстанавливать больше половины всей промышленности страны. Но благо японцы — трудолюбивый народ, поэтому они не щадили своих сил. Восстанавливать экономику непросто, да и времени на это требуется немало, поэтому среди работников различных сфер появлялись свои новаторы.
Среди них был и Тайити Оно. Он был главным инженером в Toyota Motors, а в 1949 году возглавил компанию. Чтобы определить направление, в котором стоит двигаться, чтобы повысить эффективность предприятия, он обратился к международному опыту автомобильного производства.
Для этого Тайити отправился в Соединенные Штаты на заводы Ford и General Motors, чтобы увидеть их работу вживую. Там он обнаружил, что оба производителя имеют просто колоссальные масштабы производства, что было просто не сопоставимо с мощностями Toyota Motors. Но также Тайити Оно заметил и некоторые существенные недостатки, которые тормозили производственную линию. А именно то, что работникам заводов приходилось подолгу ожидать нужные запчасти, чтобы приступить к следующему этапу сборки.
Решение этой проблемы Тайити увидел в одном из американских супермаркетов Piggly Wiggly. Он обратил внимание на то, что посетители просто брали с полок нужные им товары в нужном им количестве. То есть магазину не нужно в больших количествах тратиться на хранение или логистику. По мере того, как заканчивается тот или иной товар, директор супермаркета может заказать новую партию, которая будет свежей, и восполнит потребности покупателей.
Тайити Оно вернулся домой с новыми знаниями и принялся за разработку концепции Toyota Production System. Она до сих пор не потеряла свою актуальность. Её принципы применяются не только в автопроизводстве, но и в других сферах.

Какие проблемы Toyota решал Тайити Оно?
В процессе работы над концепцией управления, Тайити выявил 7 ключевых ошибок производства, которые были в его компании до начала оптимизации процессов.
Перепроизводство.
Автомобильное предприятие имеет сложную структуру. Оно поделено на различные участки, каждый из которых занимается решением определенной задачи. В случае с Toyota проблема заключалась в том, что пока один цех выполнял свою работу в соответствии с планом и установленными сроками, другие отставали.
Останавливать работу одной производственной линии было неэффективно, потому что тогда рабочие простаивали в ожидании, когда появятся новые задачи. Предугадать это достаточно сложно, так как на скорость производства влияет множество факторов.
Поэтому перепроизводство некоторых деталей привело к тому, что склады заполняются, но количество новых машин не становится больше. Это в свою очередь повышает уровень издержек на хранение и логистику.
Потеря времени.
Время — очень важный ресурс в любой деятельности. А если речь идет о бизнесе, то тем более. Из–за того, что некоторые участки производства работают неэффективно, это приводит к потере времени. Работники ждут сырья, деталей, когда закончится определенный цикл производства. Это отрицательно сказывается на мотивации сотрудников, а также является одной из причин возникновения брака и других проблем.
Лишние перемещения внутри предприятия.
Эта проблема возникла из–за того, что компания имела разрозненную сеть цехов производства. Чтобы передать детали на другой участок, некоторые из них сначала доставлялись на склад, а затем ехали дальше. Это и долго, и затратно, что конечно же не устраивало Тайити Оно. Требовалось оптимизировать процесс перемещения деталей, чтобы сократить издержки и увеличить производительность.
Ненужные операции.
Из–за того, чтобы были проблемы перепроизводства, повышался риск возникновения ошибок. Чем больше усилий прилагаешь к тому, чтобы выполнить изделие без брака, тем более вероятно сделать наоборот. Постоянный поток задач не дает возможности тщательно проверять качество изделия, что увеличивает долю брака.
Избыток запасов.
Эта проблема возникает не только из–за переизбытка производства, а из–за сложностей работы с поставщиками. Например, один из них продает свой товар только большим оптом от 10 тысяч деталей. Этого количества хватит на то, чтобы выпустить 10 тысяч автомобилей. Но сам по себе процесс долгий и трудоемкий. Поэтому купленные детали хранятся на складе до тех пор, пока не потребуются.
В процессе разработки автомобиля может возникнуть идея, как улучшить его конструкцию. И тогда потребность в тех 10 тысячах деталей пропадает, так как нужны уже другие запчасти. Соответственно старые нужно либо применить, либо утилизировать, либо вернуть производителю, что сложнее всего.
Лишние движения и много ручной работы.
Для работы над одной деталью сотруднику компании требуется большое количество различных инструментов. Если на столе или стеллажах нет порядка, то это приводит к лишним телодвижениям, которые так же съедают время на работу и проверку качества.
Брак.
Низкая квалификация рабочих не позволяет должным образом настроить автоматическое оборудование, чтобы сократить производственный цикл и улучшить качество выпускаемой продукции. По этой причине появляется большое количество брака, который приходится переделывать, что ещё сильнее увеличивает цикл производства и снижает эффективность.
В следующем разделе узнаем, каким образом Тайити Оно решал выявленные проблемы и как это привело к созданию новой гибкой методологии управления производством.

Как бережливое производство помогло решить проблемы Toyota Motors?
Прежде всего нужно понять, в чем заключается суть бережливого производства. Мы помним, что Тайити Оно взял в основу принцип супермаркета из США, который предлагает оптимизировать процессы и подготавливать продукты «точно в срок».
То есть, для того, чтобы выпустить один автомобиль, производится и покупается то количество деталей, которое необходимо для производства одного автомобиля. К тому же их поставка осуществляется строго к определенному сроку, чтобы не возникало простоя или наоборот не копилось избытков на складе. Таким образом удается решать проблемы перепроизводства, потери времени из–за длительного ожидания и прочие недостатки, которые мы описали выше.
Благодаря принципу работы «точно в срок» Тайити Оно удалось реализовать «вытягивающее производство». То есть один цех берется за работу только в том случае, если возникает запрос от другого цеха. По сути это стало одним из первых этапов создания бережливого производства, которым и прославилась Toyota.
Далее рассмотрим ещё несколько этапов, которые постепенно внедрялись в работу компании для оптимизации процессов.
Single-Minute Exchange of Dies (SMED).
Быстрая переналадка производства, которая позволяет компании оперативно адаптироваться под новые условия и запросы. Этот метод разработал коллега Тайити — японский инженер Сигео Синго.
SMED делит переналадку на два типа:
Внутренние действия – это те операции, которые можно выполнить после остановки оборудования или инструмента. Замена одной детали на другую возможна только в том случае, если остановить станок, иначе будет нарушена техника безопасности и может быть испорчен сам продукт.
Внешние действия – тип операций, которые можно выполнять во время работы оборудования. В процессе, когда идет обработка детали в станке, можно параллельно выполнить другую задачу, чтобы потом быстрее приступить к дальнейшей работе.
Схематически это можно отобразить следующим образом:
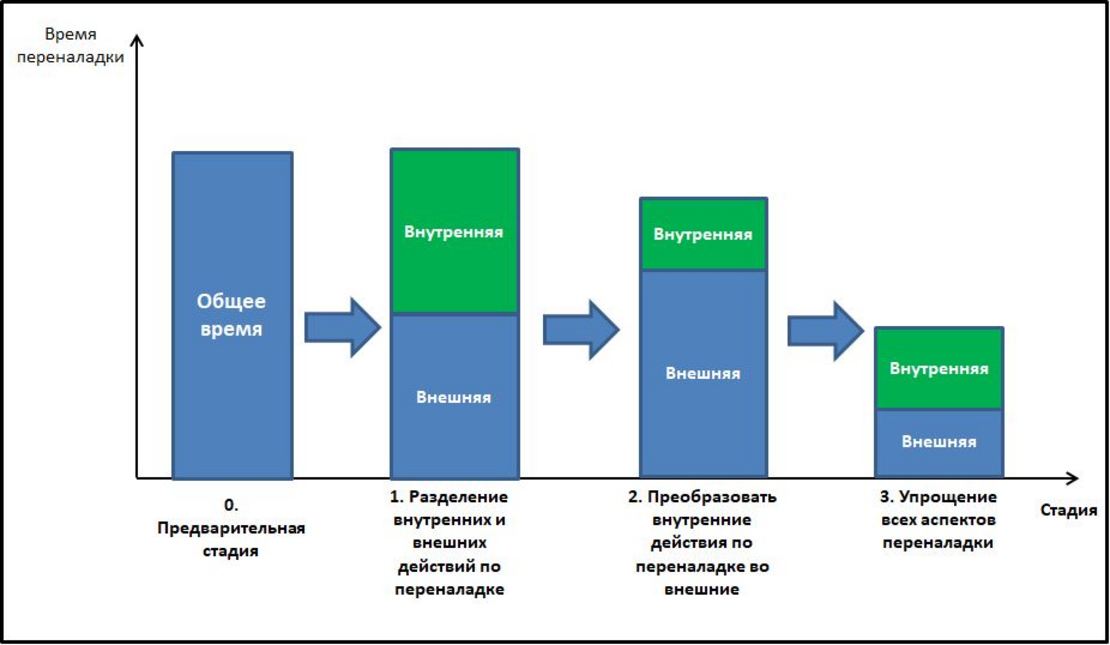
Под временем переналадки понимается промежуток времени между выходом последней готовой детали продукта из одного цеха и получением первой готовой детали из другого цеха. Если на перенастройку требуется много времени, то производство должно выпускать как можно больше деталей в течение цикла, чтобы сократить издержки. Это в свою очередь может привести к перепроизводству. Поэтому нужно стремиться к тому, чтобы сокращать время переналадки.
Кроме того, внедрение SMED позволяет всегда держать под рукой нужные инструменты и материалы для работы, что решает проблему лишних движений.
Сигео Синго выделил 8 ключевых способов оптимизации переналадки:
Разделение внутренних и внешних операций установки между собой.
Перевод внутренних операций во внешние.
Стандартизация определенных функций.
Применение функциональных зажимов или полный отказ от крепежных элементов.
Применение промежуточных приспособлений.
Проведение параллельных операций для ускорения процесса работы.
Устранение корректировок.
Механизация.
Все эти действия смогли значительно ускорить процесс производства автомобилей на заводе Toyota. Оптимизировать переналадку начали в 1949 году. Тогда в среднем скорость достигала 2-3 часов. В начале 60-х скорость переналадки сократилась до 15 минут, а спустя ещё 10 лет уже до 3 минут. Потрясающие показатели!
Про другие этапы перехода к бережному производству, расскажем в следующем разделе.

Этапы перехода на бережливое производство в Toyota Motors
Трансформация производства, а тем более, такого масштабного и сложного, как автомобилестроение, занимает много времени. Причем казалось бы, что достичь совершенства невозможно, но все таки можно к этому стремиться. Поэтому ещё одним этапом внедрения бережливого производства стало внедрение системы Канбан.
Этот процесс в Toyota начался в 1962 году. В упрощенном варианте Канбан–доска выглядела как система карточек, которые крепились к таре с деталями. Они содержали такую информацию, как наименование отдела отправителя, наименование отдела получателя, номер и количество деталей.
После того, как тара поступала в нужный отдел, из нее извлекались детали для работы. Карточка удалялась с пустого ящика, который вновь отправлялся на склад, но уже другого цеха.Так тара перемещалась между складами и отделами, и каждый из них назначал для нее новую карточку со своими задачами. В результате удалось добиться стабилизации производства и выпускать ровно то количество деталей, которое требуется в настоящий момент.
Ещё одним этапом внедрения бережливого производства стало правило 5S.
Оно потребовалось для того, чтобы решить проблему с лишними движениями во время работы и тем самым повысить безопасность производства.
Тайити Оно решил навести порядок на рабочих столах всех сотрудников, чтобы они не суетились в поисках нужного инструмента или детали. Тем самым он стремился сократить время, чтобы затем его можно было потратить на более полезные задачи. Например, на проверку качества продукта на брак.
Тайити выделил 5 ключевых шагов, каждый из которых начинается на букву С:
Сортировка.
Распределение вещей по степени важности — от нужных постоянно до бесполезных. Например, с одной стороны рабочего места могут находиться инструменты, которые требуются постоянно, а с другой стороны – отходы производства, которые нужно отдать на переработку.
Соблюдение порядка.
Принцип размещения рабочих вещей должен быть такой: можно быстро найти, легко взять и использовать, а затем вернуть на место. То есть не должно возникнуть ситуации, что в неподходящий момент нужного инструмента не будет под рукой.
Содержание в чистоте.
Соблюдение чистоты важно для того, чтобы ничего не мешало рабочему процессу. Поэтому все производственные линии имеют деление на зоны, которые убираются три раза в день: в начале смены, после обеда и в конце рабочего дня.
Стандартизация.
Каждая процедура, которая выполняется в ходе работы над выпуском автомобиля, документируется. Это необходимо для того, чтобы в будущем новый сотрудник компании мог быстро погрузиться в процесс и знать, как и в какой последовательности выполнять задачи для достижения эффективного результата.
Самодисциплина.
Это правило берет свои корни из японской культуры и по сути составляет основу 5S. Кроме того, оно базируется на подходе Кайдзен – философии, которая стремится к постоянному совершенствованию. То есть каждый сотрудник компании в полной мере осознает, что от его усилий и саморазвития зависит не только его личный успех, но и успех компании. Поэтому он всегда будет стремиться к тому, чтобы стать лучше, а также соблюдать все стандарты и правила компании.
Метод 5S направлен на то, чтобы сделать процесс обнаружения проблем и ошибок более простым и быстрым. Важно, чтобы при этом рабочие проявляли инициативу и предлагали улучшения, которые позволят ещё больше увеличить эффективность производства.
Poka-Yoke является ещё одним подходом, который позволил добиться бережливого производства. Причем он является одним из первых способов оптимизации. Его когда–то на заре компании применял Сакити Тойода. Суть заключается в том, чтобы предотвращать возможные непреднамеренные ошибки.
Именно поэтому производство выпускает ограниченное количество деталей, которое рассчитано на один автомобиль. Если обнаружится недостача или лишние крепления, то станет ясно, что допущена ошибка.
По этому же принципу существует и создается документация со всеми необходимыми инструкциями и стандартами производства. Это позволяет не только правильно собрать автомобиль, но и сделать процесс работы над ним безопасным для сотрудников.
В следующем разделе узнаем, какие результаты дали эти методы оптимизации производства Toyota.

Итоги внедрения изменений в Toyota Motors, и как бережное производство отразилось на сфере ИТ
Признания успехов долго ждать не пришлось. Ещё в начале 60-х годов прошлого века компания получила приз Эдварда Деминга. Американский ученый занимался контролем качества различных видов производств, поэтому по достоинству оценил бережливый метод японцев.
К концу 80-х годов Toyota добилась потрясающих цифр. Благодаря усилию 90 тысяч человек они смогли произвести 3,3 миллиона автомобилей в год. Чтобы понимать, насколько это быстро и эффективно, мы можем сравнить этот показатель с General Motors. Им для выпуска 5,5 миллионов машин в год требовалось усилие 775 тысяч работников. А это колоссальные издержки и высокие риски ошибок, и брака.
Философия Toyota Production System стала настолько успешной, что даже термин — «тойотизм». Причем этот подход к управлению производством не только стал популярен в ХХ веке, но не теряет своей актуальности и в наши дни.
Благодаря своему бережливому производству, к 2022 году компания выбилась в мировые лидеры автомобилестроения. Они опередили Volkswagen AG на 2,22миллионав штук проданных машин и достигли цифры 10,48 миллионов.
Теперь проведем параллели между автомобильным производством и разработкой программного продукта. Или, если быть точнее, разберемся, как бережливое производство применяется в ИТ.
Поиск узких мест и ошибок.
Команда проводит тестирование продукта на всех этапах производства, чтобы своевременно находить и устранять узкие места и ошибки. Тем самым они повышают качество продукта, а также ищут способы улучшения процессов разработки.
Итерации.
Работа над продуктом в рамках коротких спринтов сродни переналадке оборудования. Они дают возможность постоянно совершенствовать процесс разработки и тем самым сокращать цикл выпуска продукта на рынок.
Автоматизация за счет внедрения инструментов.
Если на заводе создаются стандарты и упорядочиваются инструменты на рабочих местах, то в ИТ используются различные системы. Они позволяют собирать и хранить все данные о разработке и по необходимости использовать их для анализа и отслеживания прогресса.
Стандартизация.
Так же как и в автомобильной сфере, ИТ имеет свои стандарты кода. Создаются не только какие–то нормативные документы, но и библиотеки, которые содержат готовые решения. Это позволяет сократить риск ошибок и время написания кода.
Обучение и мотивация.
Присущи для обеих отраслей. Это важно для создания экологичной рабочей среды и повышения производительности, как отдельно взятого сотрудника, так и команды в целом. Поэтому руководство поощряет инициативных и поддерживает их в саморазвитии. Чем более высокую квалификацию имеет сотрудник, тем больше пользы он принесет компании.
Не существует единого метода управления компанией, который подойдет абсолютно всем отраслям. Тем не менее, каждая организация может брать лучшее из любых успешных практик и применять их у себя. Так они смогут добиться большей эффективности.
